Avail Your Offer
Get 10% off on all accounting assignment at www.accountingassignmenthelp.com! Our experts are ready to tackle your accounting challenges and ensure top-notch results. Don't miss out on this limited-time offer to get quality help at a discounted rate. Act now and excel in your accounting studies!
We Accept
- Understanding Activity-Based Costing (ABC):
- Real-World Scenario 1: Manufacturing Company X
- Solution 1:
- Real-World Scenario 2: Service Company Y
- Solution 2:
- Expanding the Horizon of Activity-Based Costing: Real-Life Applications and Advanced Problem-Solving Techniques
- Advanced ABC Techniques:
- Solution 3:
- Real-Life Applications of ABC:
- Healthcare Industry:
- Solution 5:
- Technology Company:
- Solution 6:
- Solving Your Cost accounting Assignment with Precision:
- Conclusion:
Are you struggling to solve your Cost Accounting assignment? If so, you're not alone. Cost accounting assignments often pose challenges, especially when dealing with complex cost structures. One effective approach to address these challenges is the implementation of Activity-Based Costing (ABC). In this blog, we will delve into the practical application of Activity-Based Costing, providing real-world scenarios, example questions, and solutions that can significantly enhance your ability to solve cost accounting assignments.
Understanding Activity-Based Costing (ABC):
In the realm of cost accounting assignments, grasping the intricacies of Activity-Based Costing (ABC) is akin to unlocking a strategic tool for precision and accuracy. Unlike traditional costing methods, ABC provides a nuanced approach to cost allocation, acknowledging the diverse activities that contribute to a product or service's creation. For students tackling cost accounting assignments, mastering ABC is a game-changer.
Assignments often simulate real-world scenarios where organizations grapple with complex cost structures. ABC, with its emphasis on identifying and allocating costs based on actual activities, offers a practical solution. Through ABC, students learn to discern the direct and indirect costs associated with each activity, unraveling the true cost drivers. This understanding is crucial in decision-making, pricing strategies, and resource allocation — all pivotal aspects of cost accounting. As students navigate through ABC in their assignments, they not only solve problems but also develop a skill set essential for strategic financial management in the professional landscape.
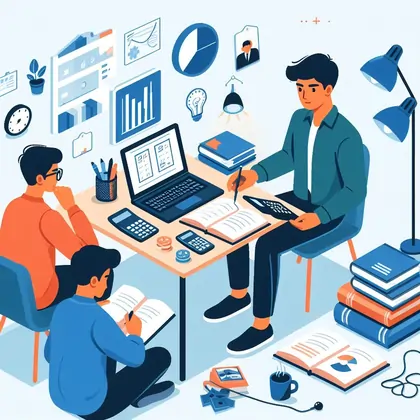
Real-World Scenario 1: Manufacturing Company X
Let's consider a manufacturing company, X, that produces customized machinery. Company X has three major activities: designing, machining, and assembly. Each of these activities incurs different overhead costs. To determine the true cost of each product, Company X decides to implement Activity-Based Costing.
Example Question 1:Calculate the Overhead Cost for Each Activity
Given the following information:
- Designing Activity Costs:$50,000
- Machining Activity Costs:$80,000
- Assembly Activity Costs: $70,000
Calculate the overhead cost for each activity using Activity-Based Costing.
Solution 1:
Overhead Rate for Designing=Designing Activity Costs/Total Units of Designing Activity
Overhead Rate for Machining=Machining Activity Costs/Total Units of Machining Activity
Overhead Rate for Assembly=Assembly Activity Costs/Total Units of Assembly Activity
Once you have calculated the overhead rates for each activity, you can then allocate the overhead costs to individual products based on the actual units of each activity consumed during production.
Real-World Scenario 2: Service Company Y
Now, let's shift our focus to a service-based company, Y, that provides consulting services. Company Y identifies two primary activities: client meetings and research. Each activity incurs different costs, and Company Y aims to use Activity-Based Costing to better understand the cost structure.
Example Question 2: Allocate Overhead Costs to Clients
Given the following information:
- Client Meetings Activity Costs: $40,000
- Research Activity Costs: $60,000
Determine the overhead cost per client for each activity.
Solution 2:
Overhead Rate for Client Meetings=Client Meetings Activity Costs/Total Client Meetings
Overhead Rate for Research=Research Activity Costs/Total Research Hours
Once you have calculated the overhead rates, you can allocate the costs to individual clients based on the actual number of meetings and research hours dedicated to each.
Expanding the Horizon of Activity-Based Costing: Real-Life Applications and Advanced Problem-Solving Techniques
In our exploration of Activity-Based Costing (ABC) for cost accounting assignments, it's imperative to delve deeper into real-life applications and more advanced problem-solving techniques. By examining diverse scenarios and employing sophisticated ABC methodologies, you can elevate your understanding and prowess in solving complex cost accounting challenges.
Advanced ABC Techniques:
Resource Driver Analysis:
Resource Driver Analysis represents a sophisticated facet of Activity-Based Costing (ABC), taking the precision of cost allocation to a whole new level. While traditional ABC relies on identifiable cost drivers such as machine hours or labor hours, resource driver analysis delves into the core resources fueling various activities, providing a more nuanced understanding of cost dynamics.
In essence, a resource driver is a factor that directly influences the consumption of resources in an activity. By identifying and aligning costs with these resource drivers, organizations gain a granular perspective on how resources are utilized, enabling more accurate cost allocations.
Example Question 3:Resource Driver Analysis for Company X
Suppose Company X identifies the resource driver for the designing activity as the number of unique design elements. Calculate the overhead cost for designing based on this resource driver.
Solution 3:
Overhead Rate for Designing=Designing Activity Costs/Total Unique Design Elements
This advanced approach allows for a more nuanced understanding of the cost structure, especially in scenarios where traditional cost drivers may not accurately capture the complexity of activities.
Activity-Based Budgeting:
In the realm of cost accounting, Activity-Based Budgeting (ABB) emerges as a strategic extension of Activity-Based Costing (ABC). Unlike traditional budgeting approaches, ABB aligns financial planning with the intricacies of specific activities, ensuring a more granular and accurate representation of costs. This method fosters a dynamic budgeting process that adapts to the evolving needs of an organization, providing a comprehensive view of resource utilization.
By integrating cost information with budgetary planning, companies can make informed decisions about resource allocation, prioritize activities that drive value, and enhance overall financial performance. Activity-Based Budgeting transcends the limitations of conventional budgeting, offering a forward-looking perspective that resonates with the dynamic nature of modern business environments.
Example Question 4:Activity-Based Budgeting for Company Y
Consider a manufacturing company specializing in custom furniture production. Traditional budgeting may allocate a fixed budget to the manufacturing department without considering the diverse activities within it. However, by implementing Activity-Based Budgeting (ABB), the company gains a more nuanced understanding of its costs.
- Identify Key Activities:
- Designing
- Materials Procurement
- Manufacturing
- Quality Control
- Packaging and Shipping
By adopting Activity-Based Budgeting, the manufacturing company gains a more accurate reflection of its cost structure, allowing for strategic resource allocation, improved decision-making, and heightened financial control. This example illustrates how ABB provides a forward-looking, activity-centric approach to budgeting, enhancing the company's ability to adapt to changing market demands and internal dynamics.
Real-Life Applications of ABC:
In practical terms, Activity-Based Costing (ABC) transcends theory, finding robust applications across industries. From healthcare, where it dissects complex medical service costs, to technology, where it refines R&D expenditure, ABC is a versatile tool. Its real-life impact extends beyond textbooks, optimizing resource allocation, pricing strategies, and informed decision-making in diverse business scenarios.
Healthcare Industry:
The healthcare sector often grapples with complex cost structures due to the diverse range of services provided. ABC proves invaluable in determining the actual costs associated with different medical procedures, patient care units, or diagnostic services. For instance, a hospital implementing ABC may identify the cost drivers for emergency room services as patient visits and intensity of care required.
Example Question 5:ABC in Healthcare
A hospital wants to implement ABC to understand the costs associated with its surgical department. Identify potential cost drivers for activities such as pre-operation preparation, surgery, and post-operation care.
Solution 5:
Conduct a thorough analysis of the surgical department activities and identify relevant cost drivers. For pre-operation preparation, the number of required tests or consultations could be a key driver, while the surgery itself might be driven by factors like complexity or duration.
Technology Company:
In the technology industry, where research and development are pivotal, ABC can shed light on the true costs of innovation. By identifying and allocating costs based on the specific R&D activities undertaken, a technology company can make more informed decisions regarding product pricing and investment in future projects.
Example Question 6:ABC in a Technology Company
A technology company is considering implementing ABC to understand the costs associated with its software development process. Identify potential cost drivers for activities like coding, testing, and debugging.
Solution 6:
For coding, the number of lines of code or the complexity of the code could be identified as relevant cost drivers. Testing might be driven by the number of test cases, and debugging could be driven by the number of reported issues.
Solving Your Cost accounting Assignment with Precision:
As you navigate the intricacies of Activity-Based Costing in real-world scenarios, it's crucial to recognize the broader implications for solving cost accounting assignments. The examples and techniques presented in this blog are not mere exercises; they represent a paradigm shift in how organizations approach cost management.
Example Question 7:Comprehensive ABC Implementation
Imagine you are tasked with implementing ABC in a manufacturing company that produces custom-designed furniture. Outline the step-by-step process, from identifying activities to calculating overhead rates and allocating costs to individual products.
To achieve a holistic understanding of Activity-Based Costing (ABC) in cost accounting, let's delve into a step-by-step guide for a comprehensive implementation:
- Identify Activities: Clearly define all activities relevant to your business. In a manufacturing context, this could encompass designing, procurement, production, quality control, and distribution.
- Assign Costs to Activities: Attribute direct and indirect costs to each activity. This involves scrutinizing expenses associated with personnel, facilities, equipment, and any other resources involved in each activity.
- Identify Cost Drivers: Pinpoint the factors influencing the costs within each activity. For instance, the designing activity's cost driver might be the number of unique design elements, while production costs could be influenced by machine hours.
- Calculate Overhead Rates:Develop overhead rates for each activity by dividing the total cost of the activity by the associated cost driver. This establishes a clear relationship between the cost and the activity's driving factor.
- Allocate Costs to Products or Services: Determine the actual consumption of each activity by specific products or services. This involves multiplying the overhead rate by the quantity of the cost driver associated with each product.
Allocated Cost=Overhead Rate×Quantity of Cost Driver
- Regularly Update and Refine: ABC is an iterative process. Regularly update cost data and refine cost drivers based on evolving business dynamics and market conditions. This ensures that ABC remains relevant and reflective of the organization's operational reality.
- Integrate ABC with Decision-Making:Leverage the insights gained from ABC in strategic decision-making. Whether setting prices, optimizing resource allocation, or identifying areas for cost reduction, the comprehensive implementation of ABC equips organizations with a powerful tool for informed decision-making.
Overhead Rate= Total Activity Costs/ Total Cost Driver Units
Conclusion:
In the fast-paced world of cost accounting, accurately assigning costs is crucial for informed decision-making. Activity-Based Costing provides a practical solution to this challenge by offering a more precise method of cost allocation. By solving your cost accounting assignment problems through real-world scenarios like those presented in this blog, you can gain a deeper understanding of how ABC works and its significance in optimizing cost management.
In conclusion, whether you are dealing with manufacturing or service-oriented scenarios, Activity-Based Costing is a powerful tool that can enhance the accuracy of your cost calculations. So, the next time you find yourself grappling with your cost accounting assignment, consider the real-world scenarios and examples provided here to guide you toward a more comprehensive and precise solution. Solving your cost accounting assignment becomes much more manageable when armed with the practical insights of Activity-Based Costing.